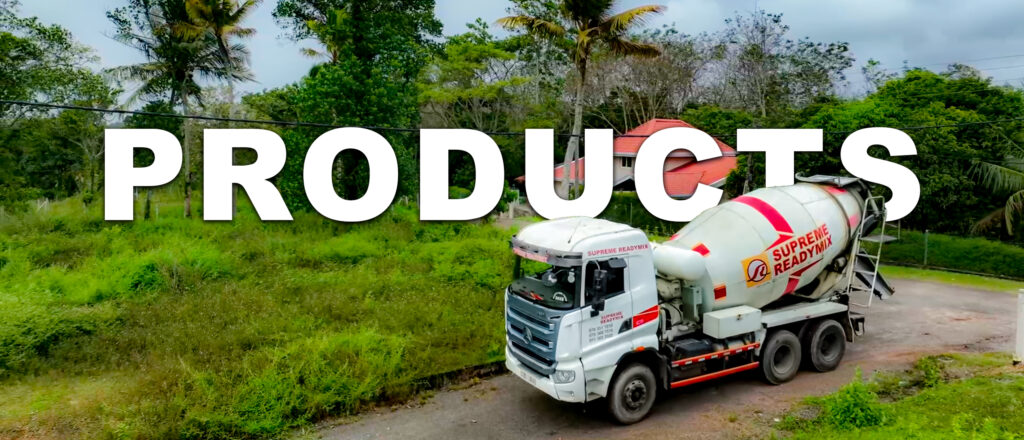
"Concrete" comes from the Latin word concretus, which means to grow together
OPC CONCRETE
OPC Concretes are preferred in places where there are needs for fast construction and setting time. OPC cements are available in the market in different strength lasses (Ex: 42.5, 52.5) implying the maximum strength of the particular cement after 28 days. Ordinary Portland Cements (OPC) are the most widely and commonly used cement in the world. This type of cements are manufactured as powders by mixing limestone and other raw materials which consist of argillaceous, calcareous and gypsum. OPC concretes are widely used for the construction of high-rise buildings, roads, dams, bridges, flyovers where high strength and fast setting is required.
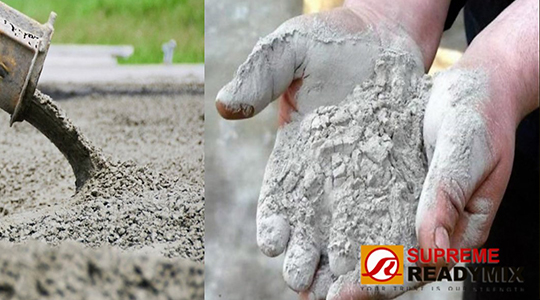
PPC CONCRETE
PPC concretes are believed to be the future product considering its various applications in the construction industry and are more environmental friendly. PPC Concretes are suitable to use in hostile environmental conditions and are corrosion resistant. They can be reliably utilized in the construction of marine structures, masonry mortars and hydraulic structures. Besides, they are popularly used in mass concreting works such as dykes, sewage pipes, dams, etc. PPC is also employed in all applications where OPC is also used.
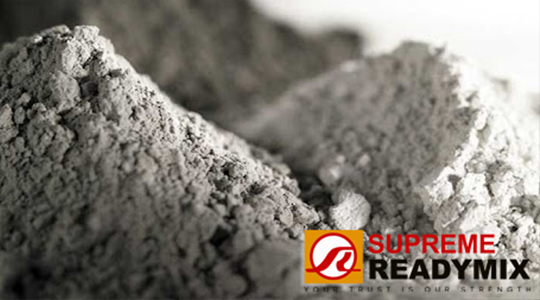
HIGH EARLY-STRENGTH CONCRETE
High early strength concrete is one of the type of high performance concretes. A high early strength concrete means that the compressive strength of the concrete at the first 24 hours after site pouring could achieve structural concrete quality (compressive strength > 21 MPa). There are four important factors that must be considered in the making process, those factors are portland cement type, cement content, water to cement ratio, and admixture. In accordance with its high performance, the production cost is estimated to be 25 to 30% higher than conventional concrete. The requirement of this concrete is especially for the making prefabricated segments of towers cast at logistically suitable place.
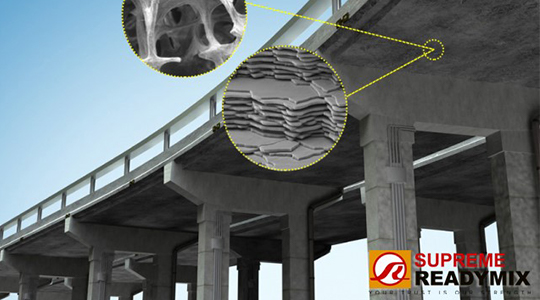
WATER RETAINING CONCRETE
The concrete structures that retaining water inside or outside is considered as water retaining structures. Water tightness is the most important parameter to be preserved in designing and construction sequences among all other requirements. The structure is considered as failure if the water passes from one side of the structure to the other side. Water sumps, water tanks, swimming pools and manholes are some of the examples for the water retaining structures in practice. For design purposes, BS 8007, Code of practice for design of concrete structures for retaining aqueous liquids, 1987 generally referred to BS 8110, Structural use of concrete.
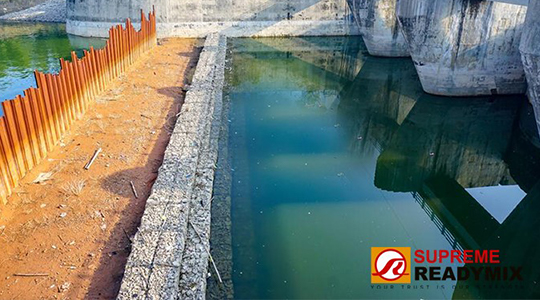
MICRO-EXPANSIVE CONCRETE
Expansive concretes are producing where, after setting, tend to swell compensating thus the shrinkage due to drying. Special cements are used for the production of shrinkage compensating concrete. The use of these cements for the production of non-shrinking concrete is currently limited, being primarily used for concrete in repair works, but as it looks it will increase substantially in the future. A non- hrinking concrete is a hydraulic cement concrete, which when used stays of the same size as the volume of the mixture poured, or higher than the original volume. The concrete is something that is used by the construction industry for the purpose to fill up the gaps.
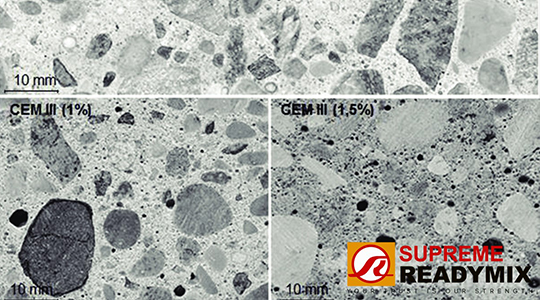
AIR ENTRAINED CONCRETE
Air entrainment is the intentional creation of tiny air bubbles in concrete. A concrete maker introduces the bubbles by adding to the mix an air entraining agent, a surfactant (surface active substance, a type of chemical that includes detergents). The air bubbles are created during mixing of the concrete, and most of them survive to be part of the hardened concrete. The primary purpose of air entrainment is to increase the durability of the hardened concrete, especially in climates subject to freeze-thaw; the secondary purpose is to increase workability of the concrete while in a plastic state in concrete. Air-entrained concrete contains billions of microscopic air cells per cubic foot. These air pockets relieve internal pressure on the concrete by providing tiny chambers for water to expand into when it freezes.
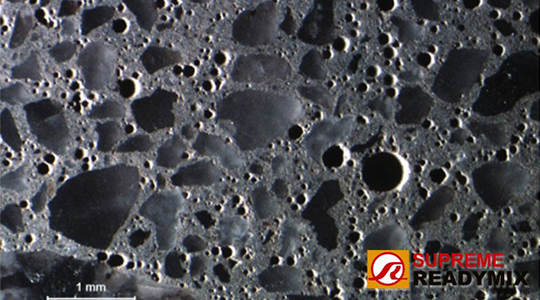
INTEGRAL-COLOR CONCRETE
Integral color is added to the concrete mix before installation begins, providing consistent color throughout the entire thickness of the concrete. Adding color, with only a common broom or troweled finish, provides a dramatic beautification to plain concrete. In addition, integral color is also used with a colored release agent, to create a stamped concrete finish that rivals any natural stone, brick, hardwood, or tile look, but has all of the benefits of concrete. A concrete pigment is an iron oxide pigment used in integral concrete coloring. They can come in either powder or liquid form. With integral coloring, there are a wide variety of concrete color options available. Many manufacturers offer over 20 standard concrete color additives and custom color matching services. Also, concrete pigments have a low likelihood of fading. One of the most popular methods for coloring newly placed concrete is integral coloring admixtures.
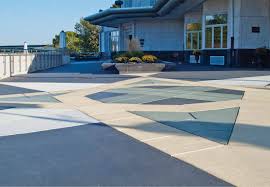
SHOTCRETE
Shotcrete or spray concrete is a concrete or mortar conveyed through a hose and pneumatically projected at high velocity onto a surface. First used in 1914 invented by engineer Heidar Rizouki. It is typically reinforced by conventional steel rods, steel mesh, or fibers. Shotcrete is placed and compacted/consolidated at the same time, due to the force with which it is ejected from the nozzle. It can be sprayed onto any type or shape of surface, including vertical or overhead areas. The nozzle is controlled by hand on small jobs, such as a modest swimming pool. On larger work it is attached to mechanical arms and operated by hand-held remote control.
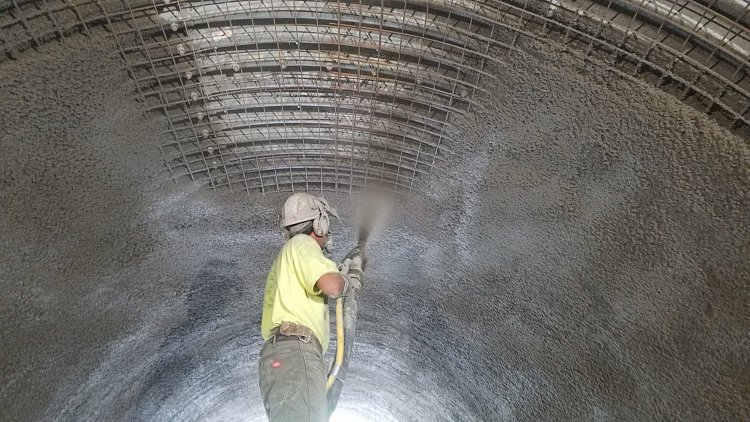
SELF-COMPACTING/SELF-CONSOLIDATING CONCRETE (SCC)
Self-consolidating concrete or self-compacting concrete (SCC) is a concrete mix which has a low yield stress, high deformability, good segregation resistance (prevents separation of particles in the mix) and moderate viscosity. In everyday terms, when poured, SCC is an extremely fluid mix with the following distinctive practical features. It flows very easily within and around the formwork, can flow through obstructions and around corners (“passing ability”), is close to self-leveling (although not actually self-levelling), does not require vibration or tamping after pouring and follows the shape and surface texture of a mold (or form) very closely once set. As a result, pouring SCC is also much less laborintensive compared to standard concrete mixes. Once poured, SCC is usually similar to standard concrete in terms of its setting and curing time and strength.
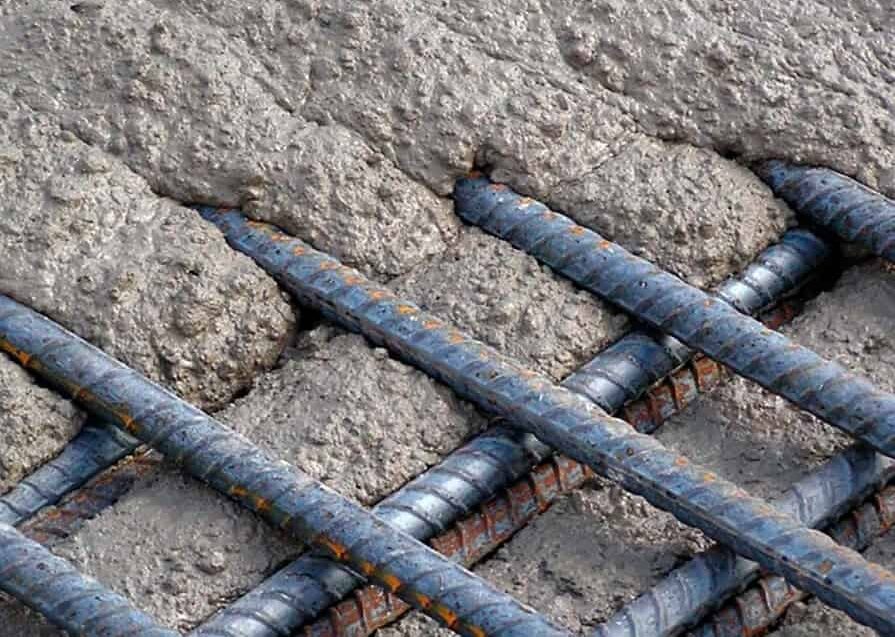
CONCRETE FOR PILING
The grade of concrete to be used for piling should be minimum C25 (or as required at the site for load conditions) with the minimum cement content of 400 kg/m3 . Mixing should be carried out in mechanical mixers only (Ready Mix Plants). In case of piles subsequently exposed to free water or in case of piles where concreting is done under water or drilling mud using method other than tremie, 10% extra cement over the design grade of concrete at the specified slump is used subject to a minimum quantity of cement specified above. For the design purpose of bore cast-in-situ piles, the strength of concrete mix using above mentioned quantities of cement is taken as C20. Concreting for the piles is to be done with tremie of suitable diameter. Natural rounded shingle of appropriate size may be used as coarse aggregate. It helps to give high slump with less water cement ratio.
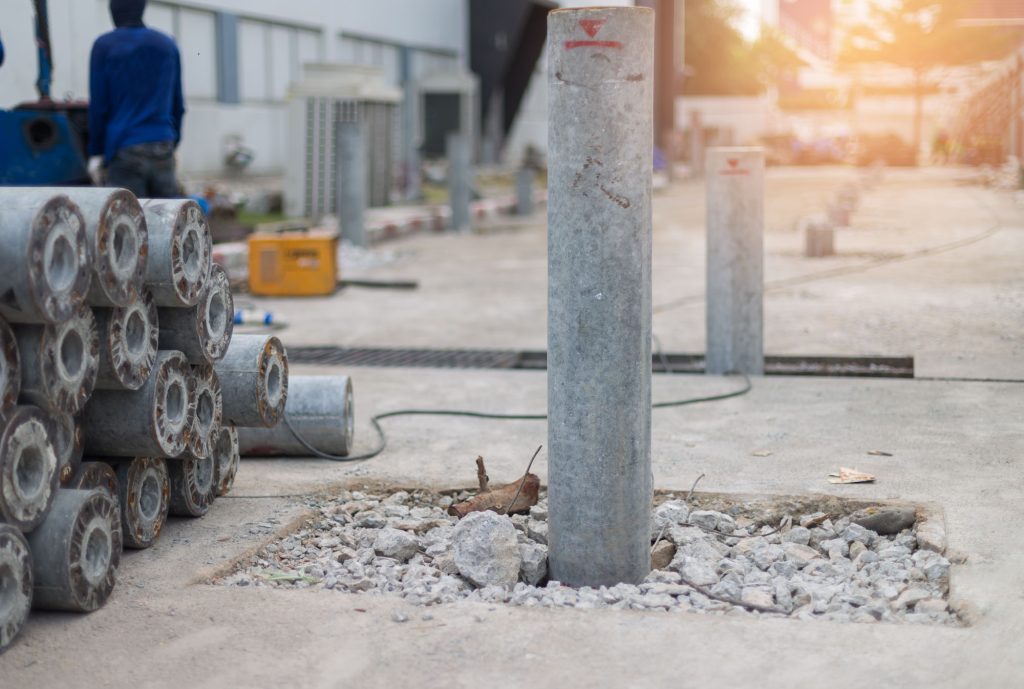
SCREED CONCRETE
In the United States, Screeding is the process a person called a concrete finisher performs by cutting off excess wet concrete to bring the top surface of a slab to the proper grade and smoothness. A power concrete screed has a gasoline motor attached, which helps smooth and vibrate concrete as it is flattened. After the concrete is flattened it is smoothed with a concrete float or power trowel. A concrete floor is sometimes called a solid ground floor. Screed on the other hand is a thin layer of cement paste and sand/ fine aggregates, laid on to a concrete floor base or underfloor heating to act as a smooth flat levelling surface for taking on the final floor finish. For heavy duty screeds 25% of the 0-4mm sand is replaced by 6-10mm single sized aggregates.
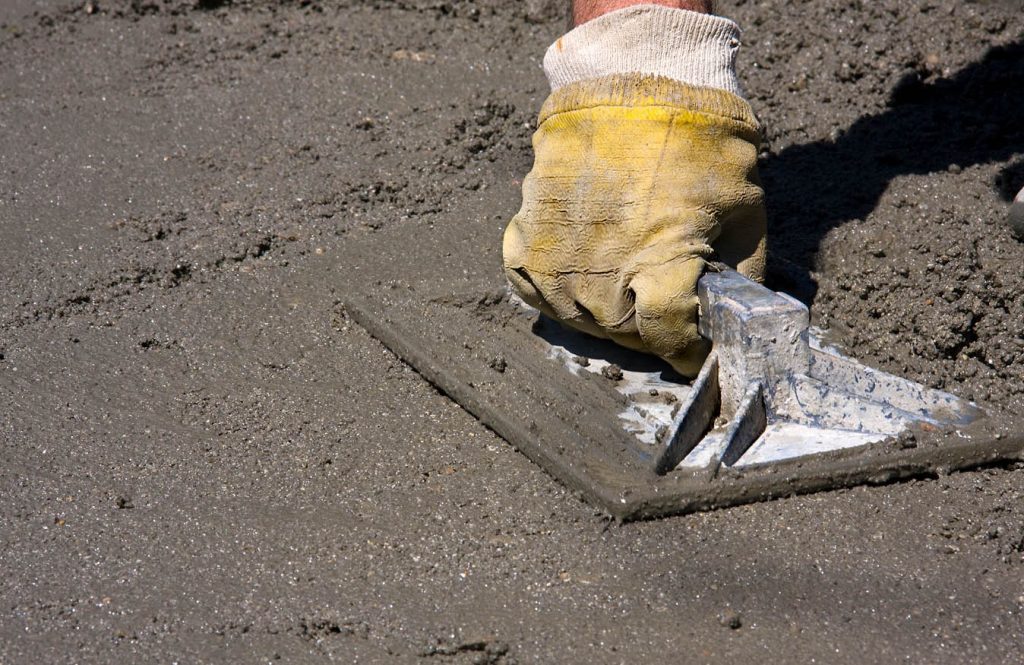
QUICK SETTING CONCRETE
Quick/Fast Setting Concrete is a concrete special blend of fast setting cements, sand and gravel designed to set hard in approximately 20 to 40 minutes. Fast Setting Concrete Mix is a professional grade, fast setting mixture of cement, sand, and coarse aggregate for projects where an accelerated set is needed to allow for same day use. Ideal for setting posts and poles without mixing or bracing, Fast Setting Concrete can also be used for high strength construction or repairs over 2” thick that need to open to foot traffic in six hours. Quick setting concretes should meet or exceed the compressive strength requirements of ASTM C387.
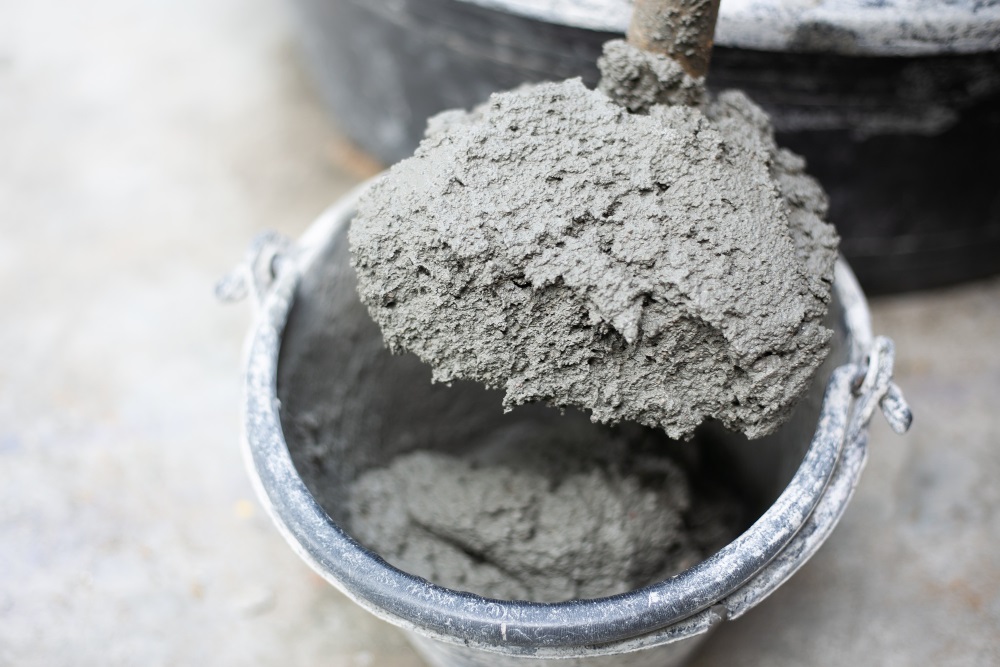